HSS Proprietary Patent-Pending Restoration
APH and GGH can get blocked in regular operation over time that cannot be effectively restored by any other method without expensive and time-consuming removal of the elements. HSS is the only organisation (as far as we are aware) that guarantees operational efficiency after the restoration within 48 hours.
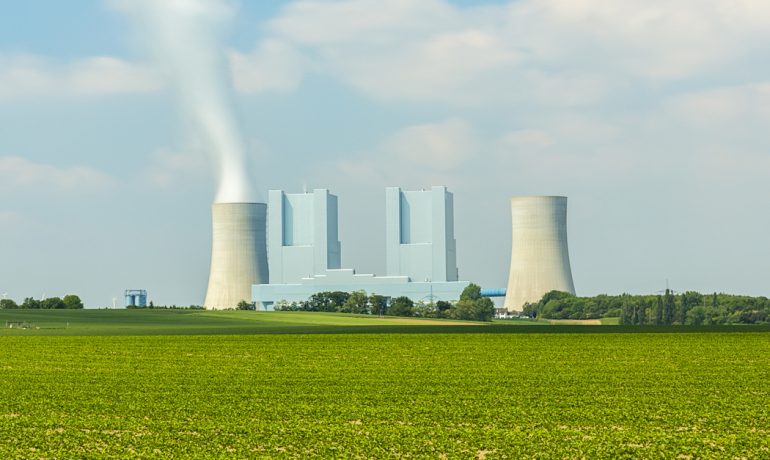
The service consists of setting up HSS proprietary specialist automated restoration equipment inside the APH or GGH. This is then connected to specialist equipment configured for restoration.
HSS industrial restoration team operates fast and independently; almost every aspect of the job is taken care of by our team. In many cases, thermal efficiency has been restored to a level not seen since the initial element installation. Restorations are typically completed within a 48 hr plant shut down. Restoration time is between 12hrs and 36hrs depending on the size of Air preheater or Gas gas heater.

Although the system is fully automated, there is considerable expertise to achieve the restoration as it requires adjustment to the condition and fouling of the APH and GGH. HSS also provides emergency restoration where we can attend almost any power station within 2 to 14 days anywhere within Asia and China.
HSS restoration process
HSS restoration process is adapted to each power station based on element condition, type of fouling, the configuration of elements and time available to carry out the restoration.
Therefore details of the restoration process specific to each power plant is available on request at contact@hssrestoration.com
Before and After HSS Restoration
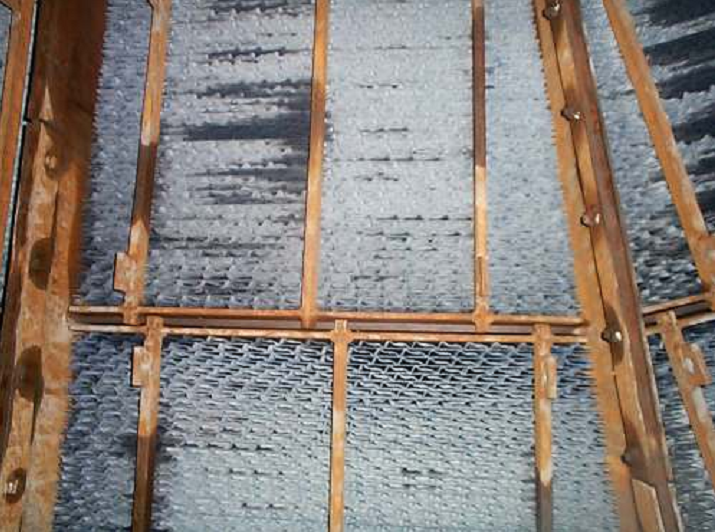
Before
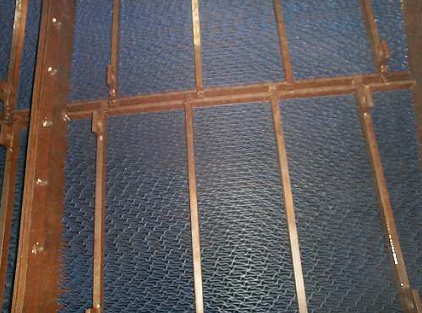
After
HSS Restoration vs Hand-held
Justifications for employing the HSS fully automated air heater and gas- gas heater restoration system.
This washing technique has successfully restored pressure drops to post commission restoration levels in virtually all cases in power stations throughout the world: proven technology developed and updated since 1984 :
HSS was instrumental in introducing computers and robotics to the restoration industry. This saves money, valuable downtime and most important of all reduces the risk to personnel in hazardous areas as unlike in the case of a hand-held operation all personnel remain outside the air heater and at a safe distance.
The automated restoration system employed by HSS is a highly effective method of recovering deep hot or cold end fouling in the shortest time possible, thus restoring pressure drops to their original commissioning levels even from almost complete blockage conditions. The nozzle is moved in steps and the speed of rotation is computer-controlled to maintain a constant relative velocity between restoration element and thus a uniform restoration of the heater matrix. Because of the level of control achieved with this automated system, the complete surface of the heater is covered during one wash cycle. This level of restoration is near impossible to achieve with a hand-held operation owing to operator fatigue and/or inability on the part of the operator to maintain the jet at a constant 90-degree angle perpendicular to the element surface.
Elements in sound mechanical condition, including enamelled elements, do not suffer damage in the process even though pressures as high as 300 bar are employed owing to the unique HSS hydraulic restoration head and nozzle design producing a high-energy water “laser” rather than merely a thin stream of water at high pressure at a very low flow-rate, as is the case with a hand-held operation.
In order for a hand-held operation to be even partially successful it is often necessary to remove the entire heater matrix (or at the very least the top and mid-packs so as to gain direct access to the top-side of the cold-end baskets). This in turn involves several weeks of lost productivity and even if this work has been factored into a scheduled plant shut-down it involves intensive manual labour with the added risk of manual handling accidents.
The time allocated for each restoration can be discussed and agreed prior to the contract directly with the HSS engineer. A maximum restoration time can then be allocated with the HSS engineer basing the restoration time on a “worst-case fouling scenario” (unless detailed pressure drop information can be provided beforehand). This restoration time may be reduced depending on plant-specific situations thus allowing the station engineer to provide a realistic time schedule to the grid and thus avoid possible penalties through the incorrect declaration of plant availability. It is unlikely that such a detailed schedule would be provided in the case of a hand-held operation.
A detailed site survey is carried out when the location is receiving the first air heater restoration or has undergone plant modification. This survey provides HSS with a detailed record of the operating, safety and restoration requirements of the power station, complying with all current legislation and international safety standards in order to offer the most effective service in the shortest time possible.
Unlike general hand-held operations, the HSS automated restoration system is a bespoke service: the restoration procedure differs between air heater design, e.g. Ljungström, Howden, or Rothemühle air heaters, gas-gas heaters, and the type of elements fitted, especially FNC elements.
Justifications for employing the HSS fully automated air heater and gas- gas heater restoration system.
This washing technique has successfully restored pressure drops to post commission clean levels in virtually all cases in power stations throughout the world: proven technology developed and updated since 1984 :
HSS was instrumental in introducing computers and robotics to the restoration industry. This saves money, valuable downtime and most important of all reduces the risk to personnel in hazardous areas as unlike in the case of a hand-held operation all personnel remain outside the air heater and at a safe distance away from the high-pressure water nozzle.
The automated restoration system employed by HSS is a highly effective method of recovering deep hot or cold end fouling in the shortest time possible, thus restoring pressure drops to their original commissioning levels even from almost complete blockage conditions. The nozzle is moved in steps and the speed of rotation is computer-controlled to maintain a constant relative velocity between jet element and thus a uniform restoration of the heater matrix. Because of the level of control achieved with this automated system, the complete surface of the heater is covered during one wash cycle. This level of reastoration is near impossible to achieve with a hand-held operation owing to operator fatigue and/or inability on the part of the operator to maintain the jet at a constant 90-degree angle perpendicular to the element surface.
Elements in sound mechanical condition, including enamelled elements, do not suffer damage in the process even though pressures as high as 300 bar are employed owing to the unique HSS jetting head and nozzle design producing a high-energy water “laser” rather than merely a thin stream of water at high pressure at a very low flow-rate, as is the case with a hand-held operation.
In order for a hand-held operation to be even partially successful, it is often necessary to remove the entire heater matrix (or at the very least the top and mid-packs so as to gain direct access to the top-side of the cold-end baskets). This in turn involves several weeks of lost productivity and even if this work has been factored into a scheduled plant shut-down it involves intensive manual labour with the added risk of manual handling accidents.
The time allocated for each restoration can be discussed and agreed prior to the contract directly with the HSS engineer. A maximum restoration time can then be allocated with the HSS engineer basing the clean time on a “worst-case fouling scenario” (unless detailed pressure drop information can be provided beforehand). This restoration time may be reduced depending on plant-specific situations thus allowing the station engineer to provide a realistic time schedule to the grid and thus avoid possible penalties through the incorrect declaration of plant availability. It is unlikely that such a detailed schedule would be provided in the case of a hand-held operation.
A detailed site survey is carried out when the location is receiving the first air heater clean or has undergone plant modification. This survey provides HSS with a detailed record of the operating, safety and cleaning requirements of the power station, complying with all current legislation and international safety standards in order to offer the most effective service in the shortest time possible.
Unlike general hand-held operations, the HSS automated restoration system is a bespoke service : the restoration procedure differs between air heater design, e.g. Ljungström, Howden, or Rothemühle air heaters, gas-gas heaters, and the type of elements fitted, especially FNC elements.
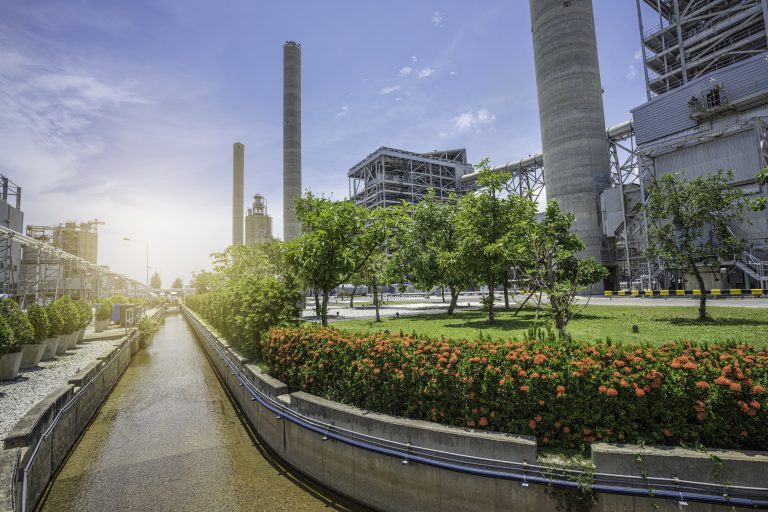
HSS Restoration Guarantee
HSS guarantee the automated air preheater restoration service. The most reliable measure of effectiveness of the restoration service is the flue gas draight loss measurements before and after the restoration service at equivalent operating conditions. In some cases the draught loss has been restored to the level when the current elements were new. The air preheater guarantee is available upon request.
HSS restoration includes
HSS 24 hour fully automated restoration service includes:
- Specialist equipment
- Consumables
- Specialist restoration personnel
Advantages of HSS Restoration
- Improved thermal efficiency
- Prolong the life of air preheater elements
- Dramatic improvement of air preheater performance
- Increase MW output of power station
- HSS provides a performance guarantee
- Reduced emissions of carbon (CO2) due to increased efficiency, leading to less fuel required to produce power.
- More efficient FGD plant by removal of fouling, therefore contributing to reductions of sulphur dioxide (SO2), particulates and nitrogen oxides (NOx).
- Restoration carried out in 24-48 hour shutdown
- Fast response time to emergency clean
- Restoration of pressure differentials
- Increased fan power
The report “Cost of air preheater fouling” is available upon request.
An example of an actual power station improvement using HSS air heater restoration system.
Source: French Power Plant 2002
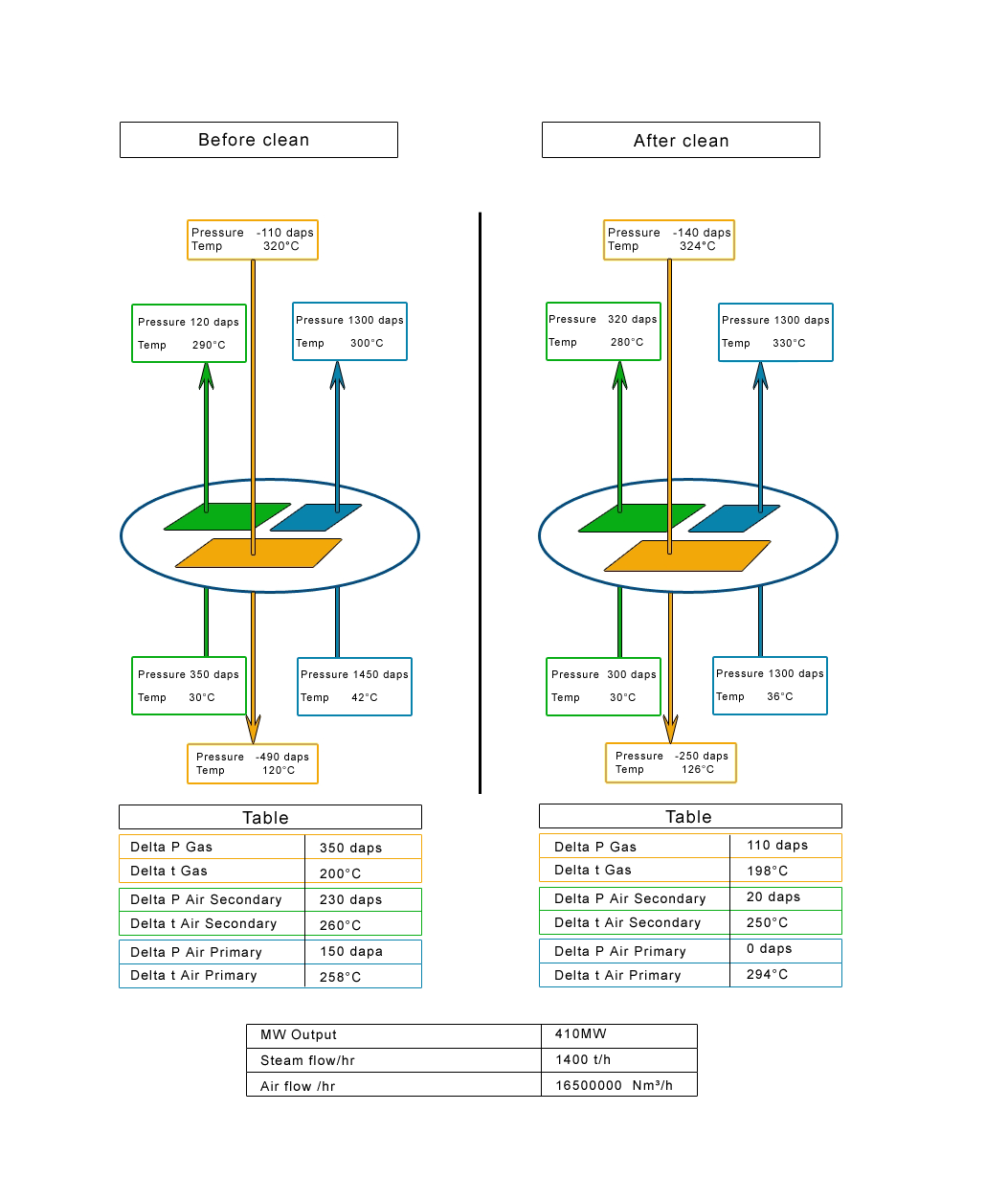

HSS Proprietary patent pending Restoration Reduces CO2 Emissions
Air Preheater pressure drops are not maintained at the design level have a significant environmental impact.
Calculations show that an increased pressure drop and leakage induced by typical air preheater fouling has increased the total CO₂ emissions from power plants by between 0.6 and 1.2%, i.e. from 950 kg/MW to 956 or 961 kg/MW, this is recoverable if APH is maintained by HSS proprietary patent pending system. This represents a reasonable proportion of the commitment to reduce emissions by 20%.
The CO₂ emission from power plants is a function of the power generated overall efficiency, fuel carbon content and calorific value. For typical solid fuels at an efficiency of 40%, the emission will be approximately 950kg of CO₂ per MW of total generation.
Increased APH pressure from fouling will inevitably increase CO₂ emissions because of the total generation required to maintain net generation. It is not unusual for APH to be operating 50% above the designed value because of fouling, e.g. 15 mbar cf 10 mbar. The fan power margin governs the limit. If fan power margins are significant enough, the air preheater’s pressure losses of twice the design value are not uncommon and considered acceptable because the perceived limit for plant operators is the point where fans become incapable of maintaining generated output.
The emission will be influenced by the amount of electricity the power plant is required to generate. Part of this is the power is expended by the fans required to force air into the boiler (Forced Draft) and remove combustion gas (Induced Draft) and exhaust to the chimney. Typically fan power is approximately 1% of generation, e.g. 5MW per 500MW. Therefore, any increase in fan power induced by the APH will increase CO₂ emission. The increase will depend on the proportion of total fan power required by the air preheaters to overcome pressure loss and supply air to gas cross leakage within the air preheater. Air preheaters consume between 30% and 60% of the total fan power, depending on the boiler design. The implications of this are that efficient air preheaters can account for 0.6% – 1.2% of the total CO₂ emissions from power stations.